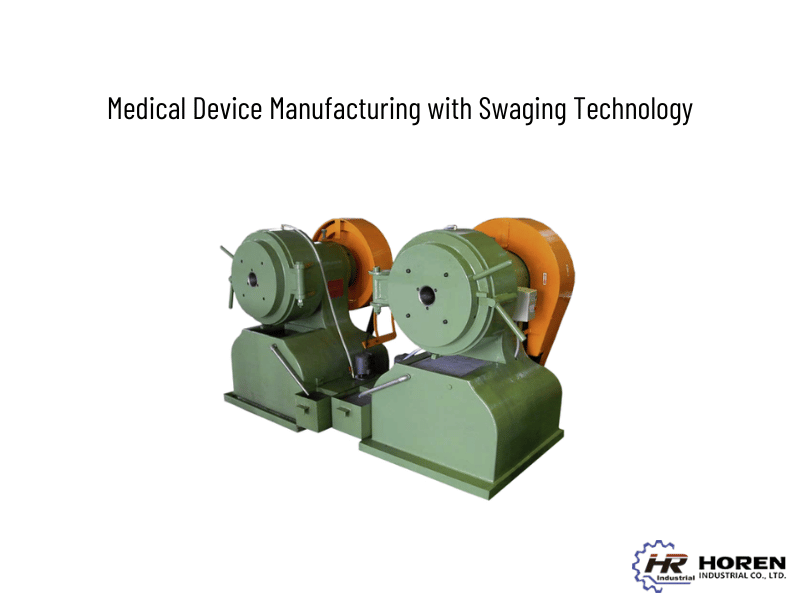
Medical Device Manufacturing with Swaging Technology
Swaging technology plays a pivotal role in the precision manufacturing of medical devices, ensuring high quality and reliability that are critical in this field. This technology involves deforming metal into precise shapes and sizes under cold conditions, preserving the integrity and enhancing the properties of the material.
The Process and Its Comprehensive Benefits
- Precision and Consistency: Swaging allows for the meticulous shaping of metal components, which is vital for intricate designs such as implants and surgical tools. The technology ensures that each component is produced with uniformity and meets exacting specifications, reducing variability and enhancing reliability in medical applications.
- Material Integrity: Unlike methods that remove material, swaging deforms metal under pressure, which maintains its strength and enhances its fatigue resistance. This is crucial for medical devices, which must endure repetitive stress and strain without failing.
- Efficiency and Cost-Effectiveness: Swaging is a highly efficient manufacturing process that speeds up production and minimizes waste. This not only reduces the cost of materials but also lowers energy consumption, making it a more sustainable choice for medical device manufacturing.
- Versatility: Swaging technology can handle a variety of metals commonly used in medical applications, including stainless steel, titanium, and specialty alloys. This flexibility allows manufacturers to use the best material for each specific application, from flexible stents to rigid orthopedic pins.
Critical Applications in Medical Device Manufacturing
- Cardiovascular Devices: Swaging is used to manufacture small, precise components such as stents and heart valves, which require high precision for proper function and longevity.
- Orthopedic Hardware: The technology is ideal for creating load-bearing implants like screws and rods that need high tensile strength and precise dimensions.
- Surgical Tools: Swaging helps in crafting finely detailed instruments used in surgery, which must be reliable and exact to ensure successful outcomes.
Advancing Manufacturing Capabilities
As the demand for more sophisticated medical devices grows, manufacturers must adopt technologies that can keep up with the need for innovation and precision. Swaging offers a robust solution by ensuring components are not only made to high standards but also produced efficiently and sustainably.
Conclusion
In the ever-evolving field of medical device manufacturing, swaging technology stands out for its ability to deliver high-quality, precise, and durable components. At Horen Industrial Co. Ltd., we are committed to leveraging this advanced technology to support manufacturers in their quest to improve patient outcomes and lead in the competitive medical device market. Our expertise and cutting-edge solutions ensure that our partners and clients receive the best in technology and service.