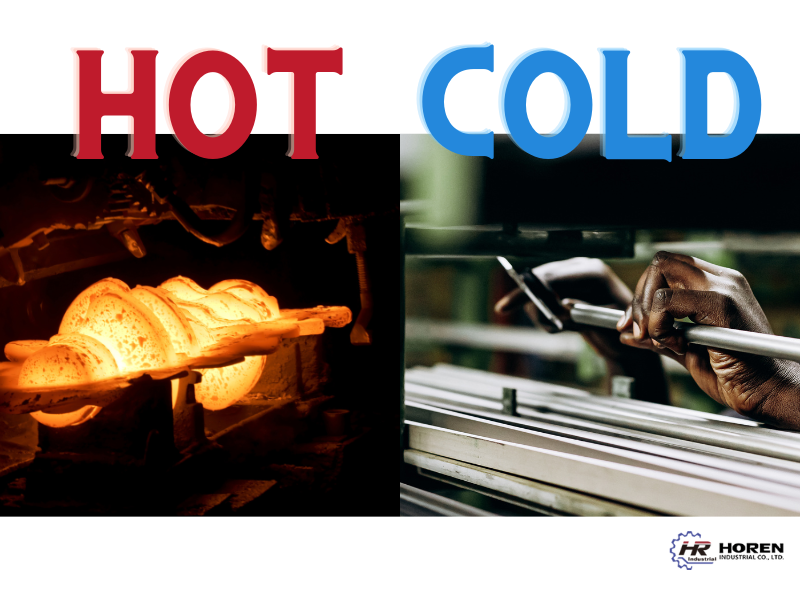
Comparing Cold Drawing and Hot Working: Applications and Selection Guide by Horen Co. Ltd.
In the realm of metal forming and manufacturing, two primary processes stand out for shaping materials into desired forms: cold drawing and hot working. Both methods offer unique advantages and serve different purposes in the industry. Horen Co. Ltd., a renowned cold drawing machine manufacturer in Taiwan, delves into these techniques to help manufacturers understand their applications and make informed choices. This article compares cold drawing and hot working, highlighting their applications and providing a guide on how to choose between them.
Cold Drawing: Precision and Strength
Cold drawing is a process employed by Horen Co. Ltd. to manufacture high-precision bars, wires, and tubes. It involves pulling the metal through a die at room temperature. This technique does not require the metal to be heated, making it distinct from hot working processes. Cold drawing is celebrated for enhancing the mechanical properties of metals, including strength, hardness, and surface finish, while also achieving closer dimensional tolerances.
Applications of Cold Drawing
Cold drawing is particularly suited for applications that require high precision and strength. The automotive industry, for instance, relies on cold-drawn products for components that demand tight tolerances and superior surface finishes, such as engine parts, suspension components, and fasteners. In the aerospace sector, the high strength-to-weight ratio of cold-drawn materials makes them ideal for structural components and hydraulic systems. Additionally, the medical field benefits from the precise dimensions and smooth surfaces of cold-drawn bars and tubes for surgical instruments and implants.
Advantages of Cold Drawing
- Improved Mechanical Properties: Cold drawing increases the yield and tensile strength of metals, making them more durable and resistant to wear and tear.
- Enhanced Surface Finish: The process results in a smooth and bright surface, reducing the need for additional finishing operations.
- Tight Tolerances: Achieving closer dimensional tolerances is more feasible with cold drawing, essential for high-precision applications.
Hot Working: Flexibility and Ductility
Hot working encompasses a variety of processes, including hot rolling, hot extrusion, and hot forging. These methods involve heating the metal above its recrystallization temperature, which significantly reduces the force required to deform the metal and increases its ductility. Hot working is beneficial for making larger or more complex shapes, as it allows the metal to be shaped more easily than in cold working.
Applications of Hot Working
Hot working is advantageous for creating large-scale and complex components where the material's ductility and the ability to undergo significant shape changes are crucial. It finds extensive use in the construction industry for structural beams, rails, and plates. The energy sector benefits from hot working for manufacturing large components such as wind turbine shafts and pipelines. Additionally, the automotive and aerospace industries utilize hot forged parts for components that require high ductility and resistance to impact, such as chassis parts and engine casings.
Advantages of Hot Working
- Increased Ductility: Metals become more pliable at high temperatures, allowing for more significant deformation without cracking.
- Reduced Strength and Hardness: This can be advantageous when the material needs to undergo further shaping or welding.
- Scalability for Large Components: Hot working is more suitable for producing large or complex shapes that would be challenging or impossible to achieve through cold working.
Choosing Between Cold Drawing and Hot Working
The selection between cold drawing and hot working hinges on several factors, including the desired material properties, the complexity of the shape, and the application's specific requirements.
- Consider the Material Properties: If high strength, tight tolerances, and a smooth surface finish are priorities, cold drawing is the preferred method. For applications requiring high ductility and the ability to produce large or complex shapes, hot working is more suitable.
- Assess the Application Requirements: The end use of the product often dictates the manufacturing process. For components that must withstand high stresses or require precise dimensions, cold drawing offers the necessary characteristics. Conversely, hot working is ideal for parts that benefit from increased ductility and are less critical in terms of surface finish and tolerances.
- Evaluate Cost and Efficiency: Cold drawing typically requires less energy than hot working, as it does not involve heating the material. However, the initial investment in cold drawing machinery and dies can be significant. Hot working, while more energy-intensive, can be more cost-effective for producing large quantities of parts, especially when the exacting tolerances of cold drawing are not required.
Conclusion
Both cold drawing and hot working play vital roles in the metal manufacturing industry, each offering distinct advantages for different applications. Horen Co. Ltd. specializes in cold drawing technology, providing high-quality machines that support manufacturers in achieving precision, strength, and efficiency in their products. Understanding the specific needs of your application is crucial in selecting the appropriate process, whether it's the precision of cold drawing or the flexibility of hot working. By carefully considering the material properties, application requirements, and cost implications, manufacturers can make informed decisions that optimize their production processes and meet the demands of their end-users.