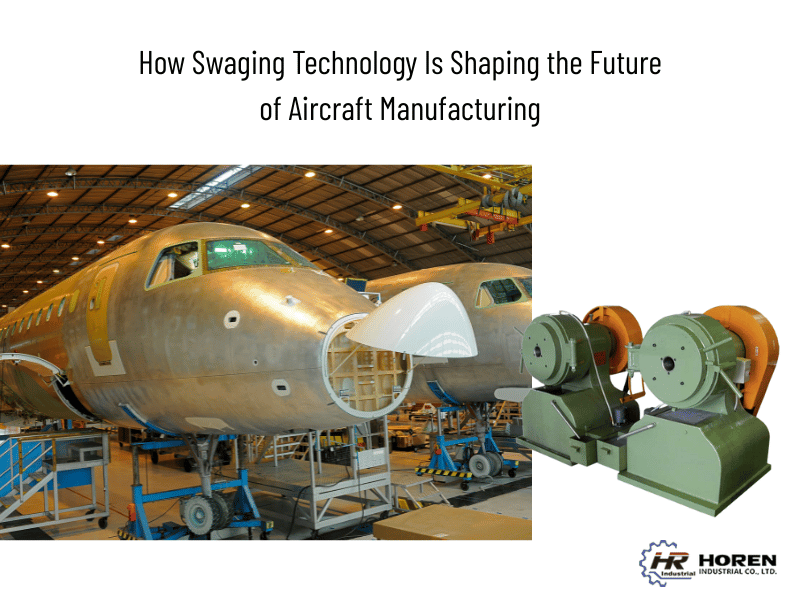
How Swaging Technology Is Shaping the Future of Aircraft Manufacturing
In an industry where every gram counts and precision is paramount, aerospace manufacturing constantly seeks out technologies that can deliver lighter, stronger, and more reliable components. One such technology is swaging — a metal forming process that has quietly revolutionized the way high-performance parts are made. From aircraft frame components to complex tubing systems, swaging plays a vital role in shaping the future of aviation.
________________________________________
What Is Swaging?
Swaging is a cold-forming metal process that changes the dimensions or shape of a workpiece by applying high pressure through a die or set of dies. Unlike machining, which removes material, swaging reshapes the material without any loss, strengthening the metal through plastic deformation and grain realignment.
There are two main types of swaging:
- Rotary Swaging: Dies rotate around the workpiece, reducing its diameter and refining its shape.
- Radial Swaging: Dies impact the workpiece from all sides simultaneously to compress and form the material.
This process is especially valuable in aerospace, where precision, structural integrity, and lightweight construction are critical to safety and performance.
________________________________________
Swaging in Aerospace: Key Applications
1. Tubing Systems
Aircraft contain extensive tubing networks for hydraulics, fuel lines, oxygen supply, and cooling systems. These tubes must be lightweight, thin-walled, and leak-proof — yet strong enough to endure pressure and vibration.
Swaging enables the formation of high-precision tube ends, ensuring tight, secure fittings without welding or brazing, which reduces overall weight and potential points of failure.
2. Fastener and Connector Production
High-strength connectors and fastening systems are essential in aircraft assemblies. Swaging is used to form solid, metal-to-metal locking connections — especially in cable assemblies for control systems. These connections are often lighter and more fatigue-resistant than traditional bolted or riveted joints.
3. Landing Gear and Engine Components
Certain parts of the landing gear and engine housings benefit from swaging, particularly when manufacturing tapered shafts, reinforced collars, or high-strength sleeves. These components must withstand tremendous loads, and swaging increases their density and fatigue life.
4. Composite Reinforcement
With the increased use of carbon fiber and other composites in aircraft, swaging also plays a role in reinforcing the metallic ends of composite tubing to allow mechanical joining or sealing without damaging the material.
________________________________________
Advantages of Swaging in Aerospace Manufacturing
• Weight Reduction Without Strength Compromise
Swaging forms metal components with minimal material use, which is crucial in aerospace, where weight savings translate directly into fuel efficiency and payload capacity.
• Improved Material Properties
The cold-forming nature of swaging enhances grain alignment, which improves strength, fatigue resistance, and impact performance — essential properties for components operating under extreme conditions.
• High Precision
Swaging machines can achieve very tight tolerances, producing parts that meet the exact specifications demanded by aerospace engineering.
• Repeatability and Cost Efficiency
For high-volume production, swaging is highly repeatable and consistent, reducing the need for secondary machining and lowering production costs in the long run.
• Material Versatility
Swaging works effectively on aerospace-grade metals such as titanium, Inconel, stainless steel, and aluminum alloys, offering flexibility in part design and functionality.
________________________________________
Swaging and Sustainability in Aerospace
As the aerospace industry moves toward sustainability, reducing material waste, energy consumption, and carbon emissions becomes increasingly important. Swaging supports these goals:
- It reduces scrap, since no material is removed.
- It requires no heating (in cold swaging), which lowers energy usage.
- It extends component life, reducing the frequency of replacements and maintenance.
In a field where environmental considerations are growing in priority, swaging provides a lean, green manufacturing solution.
________________________________________
The Future of Swaging in Aircraft Manufacturing
With advancements in automation, sensor integration, and smart tooling, swaging machines are becoming even more precise and adaptable. Manufacturers can monitor tool wear, material stress, and dimensional accuracy in real time, ensuring zero-defect production in critical aerospace parts.
Furthermore, as aircraft designs evolve to include more advanced materials and lighter structures, swaging will play a critical role in forming the hybrid metal-composite components of the future.
________________________________________
Conclusion
Swaging technology may not be the most visible part of aerospace manufacturing, but its impact is undeniable. It offers the perfect combination of precision, strength, efficiency, and material savings — all essential in the development of modern aircraft.
At Horen Industrial Co. Ltd., we’re proud to support the aerospace industry with high-performance swaging machines designed for today’s most demanding production environments. Whether you're manufacturing precision tubing, structural fasteners, or high-strength connectors, we’re here to help shape the future of aerospace — one part at a time.
If your production requires the highest standards of accuracy, strength, and repeatability, contact us today to learn how swaging can take your aerospace components to the next level.